Diamond Cutting Tools for Oil and Gas Industry from Element Six Company Syndrill
Syndrill is a product that represents a layer of polycrystalline diamonds synthesized on a hard alloy support under pressure and high temperature. The range of diamond grain sizes for Syndrill is from 20 to 40 μm, the average size of hard alloy particles is 3-6 μm, and cobalt average weight makes 13%.
The success of Syndrill with its customers is referred to the two important properties. First of all, the wear resistance of diamond layer is maintained during the course of use, and enables to solder the alloy to a bit body heavily. Secondly, the availability of hard alloy provides durability and enables to solder the alloy to a bit body heavily.
PDC cutters GTA,GES,GOS (2013/2014)
GTA
- The multimodal interface and composition of diamond mixture in combination with a minimum 5. 5 GPa pressure provides even more reasonable abrasive resistance and impact hardness at the level of previous premium cutters of Е6 GDS/GDX/GDC. It is recommended for soft to medium rocks, and also for the restoration of bits
- The axially symmetric interface is the same as on GDS/GDX/GDC cutters
- All sizes are available: 1308,1313, 1613, 1616, 1913, 1916, 1919
- Chamfer sizes:
0,4 мм 45 - DTB
0,5 мм 45 - DTС
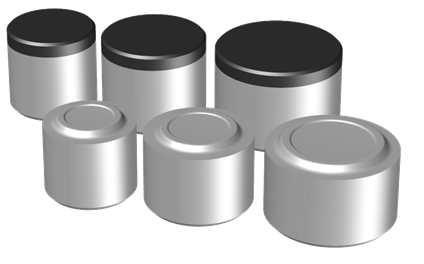
GES/GOS interface
- The new hi-tech and sophisticated interface equivalent to cutters GUDE, GLSF, GOM, GOS is applied for all premium level cutters. All standard sizes from 13 to 19 mm are available.
- The modified multimodal mixture of diamond with cobalt and tungsten provides an excellent ratio of abrasive resistance and impact hardness.
- E6 reserves the right to make changes. For example, GES and GOS cutters can be supplied with 2 types of interfaces
The wearing test – VTL abrasive resistance test
Semifinished product
- Finely or medium-grained granite
- Minimum hardness: 220 Mpa
Cutting specification
- RPM: 54 (40-160 m/min)
- Depth: 0.25 mm
- Feed speed: 4.5 mm/rev
- Cooling: water
PDC cutter
- Diamond chamfer - 0.4 mm x 45°
- Pitch: 20°
Results of VTL tests
Comments and conclusions
- Cutters GTA, GDS, GKS, GES are very similar in terms of specification, with regard to abrasive resistance and impact hardness, however the results of field tests and practice of these cutters application demonstrate greater efficiency of GKS and GES cutters application in comparison with GTA and GDS in the conditions of identical loads. GTA is characterized similar to GDS cutters in terms of impact hardness and abrasive resistance, especially with DTB/DTC chamfers on a diamond layer. GKS, GUDE and GSAH are characterized by a better wear resistance than GDS/GTA. GES cutter is a new generation of cutters that demonstrates excellent wear resistance in combination with high impact hardness.
- The composition of diamond mix, pressing and synthesis force, identical hard alloy composition are very similar on all the types of these cutters. We classify all these cutters as an average premium level.
- GES proves considerable improvement of abrasive resistance. At least, in the process of progressing wear of the cutting edge a cutter remains practically undamaged without micro spalling, and it doesn't result in the cutter's accelerated damage in the course of drilling, which is achieved by means of finer composition of diamond mix GES and the increased pressing force in comparison with GDS/GTA. The distinguishing features of this cutter are the following:
- The optimized conditions and modes of pressing
- A very good combination of impact hardness and abrasive resistance
- GOS cutters have a similar composition of diamond mix, practically the same as for GES/GKS. However, this new generation of cutters HTHP, i.e. cutters with the synthesis carried out with much higher (7 GPa) pressing force and higher temperature than for all previous cutters. Also, the share of cobalt and tungsten is changed a little. All these changes resulted in a situation where GOS massively outcompetes all other E6 cutters in terms of abrasive resistance, at the same time retaining a good impact hardness.
Test for impact resistance of PDC cutters
he conditions of test:
- load weight (Kg): 10
- Impact load (J): 20J in the beginnings of the test with increase in 5J intervals
- Hardness of anvil (HRC): 58±1
- Number of impacts: 8 repeating impacts with increased force
- Evaluation criteria: Destruction more>10% of a cutter volume
New 2015 HTHP cutters
Impact and wear-proof
New indications of E6 cutters 2015
IM-I
- IM indicates a new type of impact-resistant PDC cutters
- I indicates the next generation of PDC cutters
- IM-I эis a new generation of PDC cutters of high compression for the use in the conditions of high impact loads and vibrations for medium and hard rocks.
GP-I / P
- GP indicates the new type of PDC cutters of the general use with the increased wear resistance
- I indicates the next generation of PDC cutters
- GP-I is a new generation of PDC cutters of high compression for the use in the conditions of high requirements to low wear of cutters and sufficient impact hardness.
These cutters supplement the range of PDC cutters of E6 along with the successful cutters GOS and GES of general widespread application.
Review of premium class PDC cutters of E6 production
Syndrill code of cutters | Field of application: |
Dimensions (D-mm) |
Diamond layer thickness (mm) | Support |
SQC | General and specialized | 8, 9,5, 10 | 1.8 | WC-Co |
GTA | General | 13,16,9 | 2.0 | WC-Co |
GES | General | 13,16,9 | 2.0 | WC-Co |
GOS | General | 13,16,9 | 2.0 | WC-Co |
GP-I | General | 13,16,9 | 2.0 | WC-Co |
IM-I | Impact | 13,16,9 | 3.0 | WC-Co |
Comparison of diamond layer microstructure
GP-I / P 1613-20 | IM-I / P 1913-30 |
![]() |
![]() |
GES/GTA 1613-20 | GOS 1613-20 |
![]() |
![]() |
VTL test results (unleached): wear resistance
Test for impact resistance of cutters
- It is not easy to predict and carry out this test; fairly large number of cutters is required for objective statistics.
- The results of these tests should be considered in combination with the tests for wear (VTL) as impact hardness in process of wear of cutters in a drilling bit is the main reason for destruction of cutters.
- GP-I is characterized by a bigger impact hardness than GES/GES
- Predictably, the impact hardness of IM-I proved to be the best of all the cutters.
Comparison of wear resistance of GP-1 and GES leached by 100 microns (shallow leach)
NEW CUTTERS of E6:
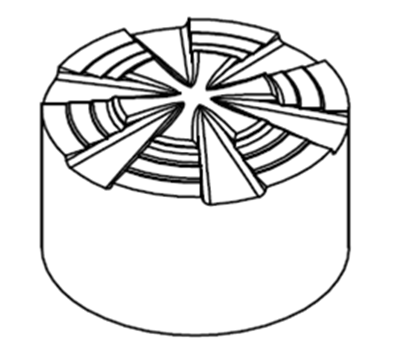
SR-1
Element Six understands perfectly well that PDC cutters make the main part of prime cost of boring tools and far from every bit demands installation of cutters of a highest premium quality.
- The application of average level quality cutters is economically justified for the drilling of soft and medium rocks, for drilling heads of all types, and also for bit restoration.
- SR-1 cutter, in the conditions of global reduction of prices for oil and gas and the need in drilling cost decrease, is designed with a view to replace in the future GES cutters with some price reduction.
- SR-1 of E6 is PDC cutter of entry premium level capable, nevertheless, to satisfy the majority of needs of clients for effective drilling of soft, medium and medium-hard rocks.
- SR-1 cutters of PDC are supplied with the guarantee that they are produced by E6 in full compliance with the highest quality standards of Element Six, especially with regard to a stable quality production
- Element Six has ISO9001 registered in 2008 and to be confirmed annually
- The quality of our materials is based on a 20 years' experience of our technical and production solutions for our oil and gas industry customers.
SR-1 WAS DESIGNED AND INTRODUCED IN PRODUCTION AT OUR NEW GLOBAL INNOVATIVE CENTER IN OXFORD, GREAT BRITAIN
SR-1 WILL BE OFFERED WITH LIMITED SIZES AND OPTIONS
Height | Chamfers | Diamond layer | Support | |
13мм |
8.00 mm
13.20 mm |
Chamfer DTB *
04.00 mm x 45⁰ |
1.8 mm |
Е6 standard support Sophisticated interface Chamfer ТС supports |
16 mm |
8.00 mm 13.20 mm |
2.0 mm | ||
19 mm | 13.20 mm | 2.2 mm | ||
![]() |
![]() |
![]() |
![]() |
EXECUTIVE SUMMARY, CONCLUSION
- Cutters SR-1 are designed for the application on soft and medium rocks, and also for non-critical locations when applied on medium-hard and hard rocks, for example in the centre of a bit, and in the locations other than a so-called "shoulder zone".
- Cutters SR-1 provide more effective alternative to the highest premium level cutters (GOS, IM-1, GP-1) if the requirements for boring tools penetration are not critical and not a priority.
- Cutters SR-1 are produced by E6 with the observation of the highest quality standards.
- The diamond layer of SR-1 is appropriate for the use in bits, it is very similar to cutters of the GES series in terms of structure and pressing force, and is suitable practically for all types of application.
- After the research of SR-1 properties of shock and abrasive resistance of shallow-leached cutters there was made the conclusion about their near-complete identity to GES cutters with marginally lower price for SR-1.